Why Combustion Research?
Why Combustion Research?
Why Combustion Research?
Why Combustion Research?
Spiral Low Mass Radiant Tubing
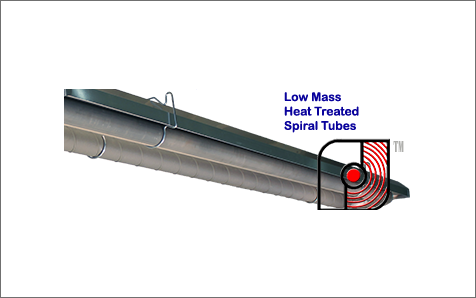
Dry Tube System
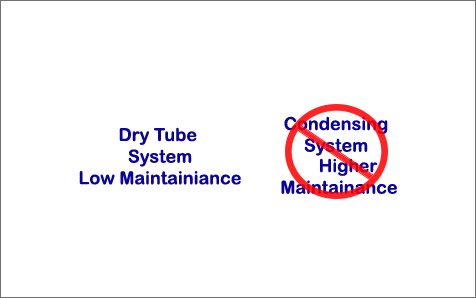
No Filters
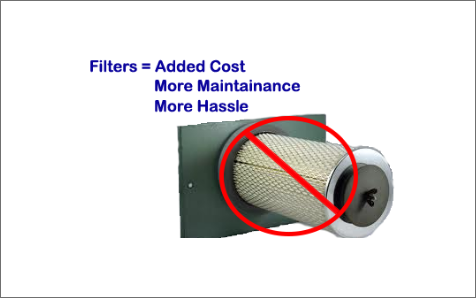
Optimal Radiant Tube Length and BTU Input
The objective of a low intensity radiant tube system is to convert the highest percentage of gas-fuel into Infra Red energy. This Infra Red energy is absorbed by the building’s concrete slab as well as the materials and items within the building. It is this absorbed energy that is stored and re-radiated to the interior of the building which provides the feeling of unparalleled comfort. In order for the building to absorb the optimum amount of energy, it is important to maintain an acceptable “Optimum Ratio of BTU Input to Radiant Emitter Tubing.”
Radiant heating systems manufactured by Combustion Research Corporation have been engineered and designed with the emphasis for “Optimum Efficiency.” Short radiant tube length, high input systems — which have become prevalent — conceal their additional operating costs. By reducing their tube lengths and increasing the BTU per hour input, the up-front costs are generally reduced. However, the trade off is lower system efficiency that requires additional BTU input to replace the wasted energy these short tube systems create. This in turn drives up the operating costs. Pre dilution exhaust temperatures in excess of 450° F have been seen. The exhaust temperature should not require dilution air for a well-designed radiant system. An “Optimum” radiant tube system will incorporate enough radiant emitter (tubing) which will deliver the maximum efficiency while striving to produce an effective “Optimum Ratio of BTU Input to Radiant Emitter Tubing.”
Spiral Low Mass Radiant Tubing
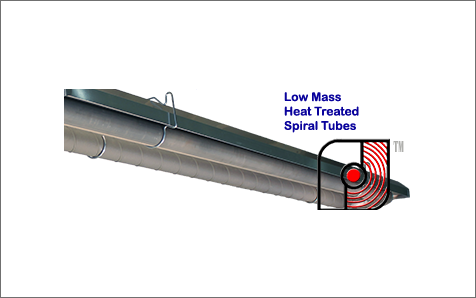
Dry Tube System
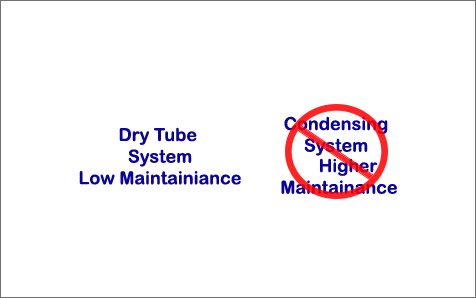
No Filters
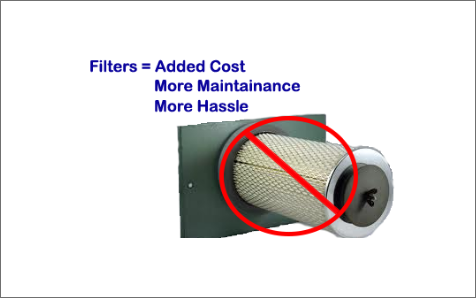
Optimal Radiant Tube Length and BTU Input
The objective of a low intensity radiant tube system is to convert the highest percentage of gas-fuel into Infra Red energy. This Infra Red energy is absorbed by the building’s concrete slab as well as the materials and items within the building. It is this absorbed energy that is stored and re-radiated to the interior of the building which provides the feeling of unparalleled comfort. In order for the building to absorb the optimum amount of energy, it is important to maintain an acceptable “Optimum Ratio of BTU Input to Radiant Emitter Tubing.”
Radiant heating systems manufactured by Combustion Research Corporation have been engineered and designed with the emphasis for “Optimum Efficiency.” Short radiant tube length, high input systems — which have become prevalent — conceal their additional operating costs. By reducing their tube lengths and increasing the BTU per hour input, the up-front costs are generally reduced. However, the trade off is lower system efficiency that requires additional BTU input to replace the wasted energy these short tube systems create. This in turn drives up the operating costs. Pre dilution exhaust temperatures in excess of 450° F have been seen. The exhaust temperature should not require dilution air for a well-designed radiant system. An “Optimum” radiant tube system will incorporate enough radiant emitter (tubing) which will deliver the maximum efficiency while striving to produce an effective “Optimum Ratio of BTU Input to Radiant Emitter Tubing.”